The metering pump is a special volume pump that can meet the requirements of various strict process flows, and the flow rate can be adjusted steplessly in the range of 0-100% to transport liquids (especially corrosive liquids). Metering pumps are also called metering pumps or proportional pumps. The metering pump is a reciprocating positive displacement pump for accurate metering. It usually requires the stability accuracy of the metering pump to not exceed ±1%. With the continuous development of the modern industry towards automation and remote automatic control, the advantages of the metering pump and the wide adaptability of the medium (liquid) are particularly outstanding.
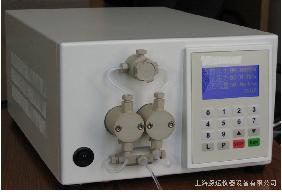
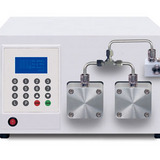
Definition of metering pump The metering pump (jì lià ng bèng) is also called a metering pump or a proportional pump. The metering pump is a need to meet various rigorous process, the flow rate can be steplessly adjusted in the range of 0-100%, used to transport liquids (particularly corrosive liquids) a special displacement pump.
According to the overcurrent part
(1) plunger, piston type (2) mechanical diaphragm type (3) hydraulic diaphragm type
2. According to the driving method
(1) Motor drive (2) Electromagnetic drive
3. According to the way of working
(1) Reciprocating (2) rotary (3) gear type
4, according to pump characteristics (1) extra large base (2) large base (3) middle base (4) small base (5) microcomputer base
Other classification methods: electric control type, air control type, heat preservation type, heating type, high viscosity type, etc.
1. Exports are higher than imports, avoiding siphon
2. Pump head and injection valve require vertical installation
3. The attached pipe fittings can be tightened by hand. Do not use tools; do not use raw tape at the thread.
4. Power supply voltage is stable and grounded
5. The installation environment is clean and spacious, well ventilated
Analysis of common faults in metering pump measurement
1) The metering pump is not properly sucked
Rotate to the 100% position of the stroke length. This allows the entire set of components to be rotated to the back plate leakage drain hole to align with the bottom end of the pump. Adjust the hydraulic end and diaphragm to the proper position during pump operation.
For reaction time, the pulse duration may not be long enough. The flow monitor pulse width extension can be activated relative to a standard pulse width of 80 msec, increasing the pulse width to 300 msec. Activate the smart transfer switch, remove the cover of the fixed circuit board, and remove the jumper X-1. This activates the extended function and allows more time before the fault indication.
The metering pump is installed from the exhaust pump head and uses self-priming aspiration. Keep the aspiration line as short as possible.
2) Dismantling the metering pump diaphragm
When you remove the old diaphragm, you often have trouble. Now give some additional advice on how to remove the old diaphragm.
1. After the pump head is loose, adjust the stroke length to 0% before removing the pump head. It is possible to ensure that the electromagnetic shaft has sufficient pressure to keep its connection stable so that the diaphragm can be unscrewed.
2. Pull the hydraulic end outward to disengage the screw from the socket. Grab the liquid end and rotate it counterclockwise. With a little resistance, you can unscrew the diaphragm.
3. Metered chemicals may crystallize at the hydraulic end, rendering the check valve ball and seat not working properly.
4. There may be a gas leak at the suction end of the metering pump. The suction side connection on the hydraulic end may be missing the O-ring or the suction valve connection is loose.
3) Metering a high-viscosity medium with flow monitoring, and receiving a flow failure indication signal during the liquid introduction process. How can this be solved?
Move the hydraulic end by loosening the 4 pump head screws. Rotating the stroke length to 0% and grasping the hydraulic end, then sliding out of the screw hole, the screws do not touch them, but also hold the back plate and diaphragm. Then turn the part counterclockwise, with a little resistance, the diaphragm will loosen from the electromagnetic shaft. If the diaphragm is not loose yet, use some lubricant on the contact surface of the diaphragm and the electromagnetic shaft. After a few minutes, gently tap the diaphragm with a plastic hammer. Then proceed again as described above.
4) How to prevent the metering pump stroke positioning motor from burning?
1. Remove the 4 screws that secure the pump head. The screw is located on the back of the metering pump.
2. See if a drain is installed and the drain valve is closed? The drain valve needs to be opened during the introduction of the metering pump. Note: Not all metering pumps have a drain valve.
3. Install the pump head after the diaphragm has been installed and the backing fluid drain hole is in the vertical position. Make sure the suction valve is aligned with the leak drain hole and the screw on the hydraulic end is aligned with the corresponding 4 holes.
5) Is the flow of the hydraulic metering pump small or inaccurate?
1. Unscrew the bleed valve in the three valves.
2. Fully replenish oil through the charge valve.
First, determine the pressure: the rated pressure of the selected metering pump is slightly higher than the actual maximum pressure required, generally 10 to 20% higher. Don't choose too high, too much pressure will waste energy, increase equipment investment and operating costs.
2. Determine the flow rate: The selected metering pump flow rate should be equal to or slightly larger than the required flow rate of the process. The use range of the metering pump flow rate is preferably 30 to 100% of the rated flow rate of the metering pump, and the repeating reproduction accuracy of the metering pump is high. Considering the economical and practical, it is recommended that the actual required flow rate of the metering pump be 70 to 90% of the rated flow rate of the metering pump.
Third, determine the pump head (hydraulic end) material: After the specific model specification of the metering pump is determined, and then select the material of the over-current part according to the properties of the over-flow medium, this step is very important. If improperly selected, it will cause corrosion damage of the medium. Overcurrent components or media leaks contaminate the system, etc. In serious cases, it may also cause a major accident.
Other aspects: When selecting a metering pump, you also need to consider the accuracy level of the metering pump required. The higher the level of accuracy, the higher the investment. The general working temperature of the metering pump is -30~100°C, and the special metering pump has a wider working temperature range (such as the high temperature liquid metering pump with insulation jacket, the conveying temperature can reach 500 °C). For the particle size of the medium, it should be less than 0.1mm. For media larger than 0.1mm, the overcurrent structure of the pump can be changed to meet the needs. For the viscosity of the medium, generally should be 0 ~ 1000mm / s, the special metering pump can reach 6000 mm2 / s, the flow rate of the mechanical diaphragm metering pump is the maximum flow measured under the rated pressure (water delivery at room temperature) When the pressure drops, the output flow rate will be higher than the calibration.
Veterinary Soluble Powder
Norfloxacin Nicotinic,Veterinary Soluble Powder,Doxycycline Hcl Powder,Norfloxacin Nicotinic Soluble Powder
Shandong Unovet Pharmaceutical Co.,Ltd. , https://www.unovetcn.com